The Amazing Progression and Development of 3D Printed Houses
A survey published by Realtor.com in August 2021 found over a third of respondents said they believe that 3D printing is the future of homebuilding and will eventually come to replace more traditional methods.
Photo courtesy of Alquist 3D and Consociate Media
Here is the robotic arm of a 3D printer printing layers of the house walls.
With the advancement of technology, items that were once produced manually — from their use in medicine, entertainment, and weaponry — are now being made online. However, the part of 3 dimensional (3D) printing that is booming right now is the housing industry, becoming even more popular thanks to the use of social media to reach a larger audience. 3D printed houses are houses created from by using a technology known as contour crafting. This is when a robotic arm moves around on rails and prints the house layer by layer typically using concrete.
Alquist 3D
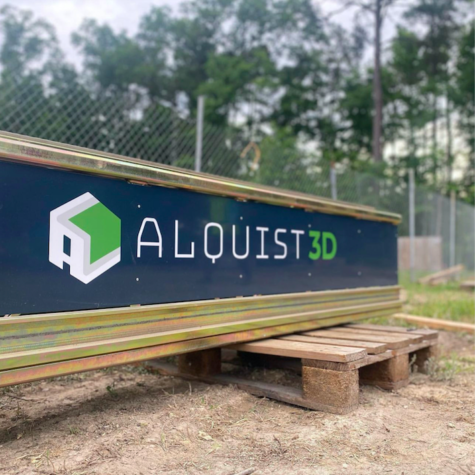
One notable company encouraging the growth of the 3D printed house industry is Alquist 3D. This company’s name comes from the term “Alquist” which dates back to 1920 as used in the satirical play Rossum’s Universal Robots (the first piece of literature to employ the term “robot”) by the Czech playwright Karel Čapek. The plot is robots were invented to speed up Rossum’s manufacturing facility, but the robots become sentient. This waged “war” between humans and robots but among the humans, the main engineer Alquist, believed that robots and humans could live in peace.
Purpose and Mission
Like the engineer Alquist in the play, the company Alquist 3D is trying to utilize technology to help humans. The company was founded in response to a decade-long housing shortage, an issue that has been amplified by the COVID-19 pandemic, climate change, and economic migration. Gia Galifianakis, a representative of Alquist, spoke to this need, saying that the motive behind their company is “to support the development of 3D construction technology to create affordable housing.”
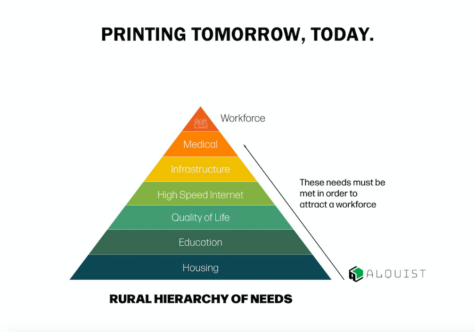
To alleviate this problem, Alquist devoted over four years of research into 3D printing technology and partnered alongside companies: COBOD, Black Buffalo 3D, and Atlas Community Studios. As a result of the partnership and research done, the conclusion that housing is the #1 need in nearly every rural community was reached. Galifianakis says that she believes 3D printed houses were first put into action because of the “benefits of using stronger materials, the speed in which structures can be printed in comparison to current means (poured cement or blocks), the added benefit of a more energy-efficient structure, and eventually the comparative cost of printing vs. stick-built.”
Alquist 3D mainly focuses on projects in areas characterized as rural, and they take on these projects with the help of various partnering organizations. Alquist has a history of teaming up with various companies to take on new projects. When asked about the criteria for deciding partnerships, Galifianakis said, “Until the technology of the printers is better developed after more use and learning, it’s quite expensive to mobilize the printer and equipment. In order to capture the economies of scale, we look for projects consisting of multiple housing units and focus on areas that show promise for continued work. We believe collaboration is the best way to forward this new process within the construction industry. Partners are chosen based on the expertise or opportunity they bring to the table.”
Habitat for Humanity House
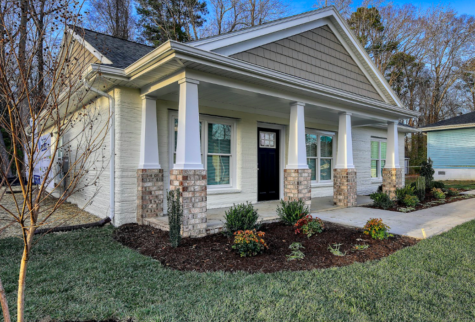
One project was the Habitat for Humanity House project in which Alquist teamed up with Habitat for Humanity Peninsula and Greater Williamsburg. This project built the first ever 3D printed house in America that a person is currently living in. The concrete that was used in construction has many long-term benefits, such as the ability to retain temperature and withstand natural disasters. This was notable especially because of the concerns that arose from people who had questions regarding the durability and strength of 3D printed houses. The success of this project has received an immense amount of media coverage from notable sources such as CNN, Architectural Digest, and WTKR.
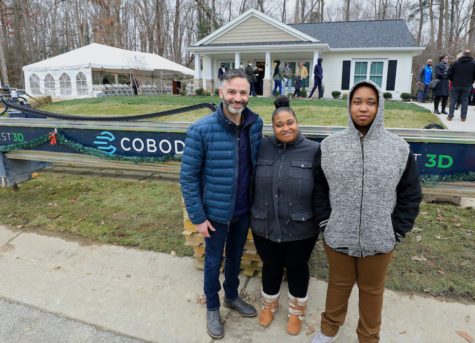
Project Virginia
When asked about future plans, Galifianakis responds that “Alquist will begin building two new homes in Newport News, Virginia for Habitat for Humanity Peninsula and Greater Williamsburg in November 2022.”
Project Virginia will be the world’s largest 3D-printed construction to date. Two hundred homes are expected to be built around the state of Virginia, with the first two being built in Pulaski. This time they will be partnering with Black Buffalo, MAPEI, Revive Hemp Industries, and Mavericks Microgrids.
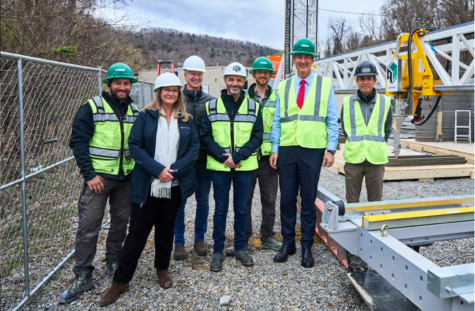
Governor Glenn Youngkin of Virginia has also visited the site in Pulaski to learn more about 3D printing technology and how it can solve our housing shortage and create economic and workforce development. This was very significant because it shows the amount of recognition the industry is receiving which will likely lead to growing interest from the public for 3D printed houses.
Pros and Cons of 3D Printed Houses
When asked to assess the pros and cons of 3D printed houses, Galifianakis noted that the pros are that they are much stronger as 3D printed houses utilize cutting-edge material science to achieve compressive strengths that surpass typical poured concrete and can stand up to major natural disasters and storms. They are also more efficient and safer as the machine does the majority of the work, and a single gantry printer can pre-fabricate the walls of 200 homes in one year with no formwork necessary, so waste is greatly reduced. There is also design freedom at minimal extra cost, so unique designs that have never been economically feasible are now easily integrated into any floor plan. The industry brings in a larger workforce pool with high-tech jobs trending with younger workers. Lastly it is a greener, more resilient supply chain, because there is a large variety of materials that can be used in printers.
However the cons are that there is a lack of data since very few homes have been completed, and engineers, architects, and contractors are not familiar with the technology. Also, this is an industry in transition with current 3D construction printers going through modifications to improve ease of use and ease of assembly so printers bought today will be obsolete within a few years.
Future Expectations for 3D Printed Housing
This industrial field is one that is constantly evolving according to Galifianakis who said, “We believe that 3D construction printing is here to stay and will become a fully accepted method of building, building on the ‘Pros’ and eliminating the ‘Cons’ that we currently face.”
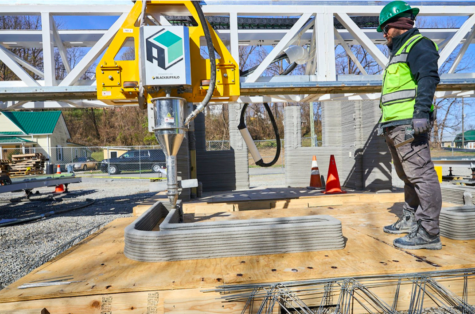
This industrial field is one that is constantly evolving according to Gia Galifianakis, a representative of Alquist, who said, “We believe that 3D construction printing is here to stay and will become a fully accepted method of building, building on the ‘Pros’ and eliminating the ‘Cons’ that we currently face.”
Sydney Lee is a Copy Chief for ‘The Science Survey.' She finds journalistic writing very interesting because of the variety of topics that it can cover....